In the aerospace industry, aircraft safety and structural performance are paramount. The airframe, including the fuselage, wings, and empennage, must endure immense stresses throughout an aircraft’s lifecycle, from fluctuating aerodynamic forces and cyclic pressurization to harsh environmental conditions.
To validate structural integrity, meet regulatory requirements, and enhance performance, airframe structural testing is a critical stage in both aircraft design and production.
This process includes comprehensive assessments such as fuselage structural testing, wing structural testing, and empennage structural testing. Engineers evaluate stress, strain, fatigue life, and load-bearing capabilities using advanced tools. Precision load cells, multi-axis force sensors, and miniature strain gauges are instrumental in collecting high-fidelity data during these tests.
Yet, challenges persist - ensuring measurement accuracy, managing calibration complexity, and integrating sensors on composite structures demand expert solutions. Overcoming these obstacles requires specialized sensor technologies and optimized testing methodologies that deliver consistent, reliable, and repeatable results.
By leveraging state-of-the-art sensor systems, manufacturers can conduct robust aircraft structural testing that supports safer, lighter, and more efficient aircraft designs for the future.
IMPORTANCE SENSORS IN AIRFRAME STRUCTURAL TESTING
Modern aircraft structures must endure years of operational stress under complex flight and environmental conditions. This makes airframe structural testing, including: fuselage structural testing, wing structural testing, and empennage structural testing, an essential part of the development process.
Key reasons for comprehensive structural testing include:
Structural Durability Validation
Identifying fatigue behavior and detecting potential failure points in key components like the fuselage, wings, and empennage before the aircraft enters service.
Regulatory Compliance
Demonstrating conformance with rigorous international safety standards, including those set by the FAA (Federal Aviation Administration), EASA (European Union Aviation Safety Agency), and ASTM International.
Weight Optimization and Performance Enhancement
Enabling the use of lightweight composite materials while maintaining structural integrity to improve fuel efficiency, payload capacity, and overall flight performance.
Regulatory bodies require exhaustive aircraft structural testing, including static and dynamic load testing, fatigue life analysis, and real-time stress monitoring. These tests ensure that all parts of the airframe meet safety and operational requirements across their service life.
CHALLENGES IN AIRFRAME STRUCTURAL TESTING
While essential to aircraft certification and safety, airframe structural testing - especially fuselage structural testing, presents several technical and logistical challenges. These challenges can impact the accuracy, efficiency, and reliability of testing programs for components including the wings and empennage.
1. Limited In-House Resources
Many aerospace organizations lack the dedicated personnel, specialized equipment, or domain expertise required to conduct end-to-end structural testing. As a result, they often rely on external partners or advanced turnkey solutions to perform aircraft structural testing at the necessary scale and precision.
2. Accuracy and Calibration Integrity
High-precision measurements of load, strain, and stress are fundamental to meaningful structural durability validation. However, incorrect sensor placement, improper data acquisition configurations, and poor calibration practices can lead to compromised results, undermining both safety assessments and regulatory compliance efforts.
3. Fatigue Resistance and Overload Protection
During fuselage structural testing and wing fatigue analysis, sensors must endure thousands of load cycles without degradation in performance. Ensuring long-term sensor durability and maintaining measurement fidelity over extended periods is a significant engineering hurdle.
4. Bonding and Sensor Placement
Effective strain measurement depends on precise bonding techniques. Issues like misalignment, poor surface preparation, or use of unsuitable adhesives can result in sensor failure or inconsistent readings—especially in composite materials common in today’s lightweight airframes.
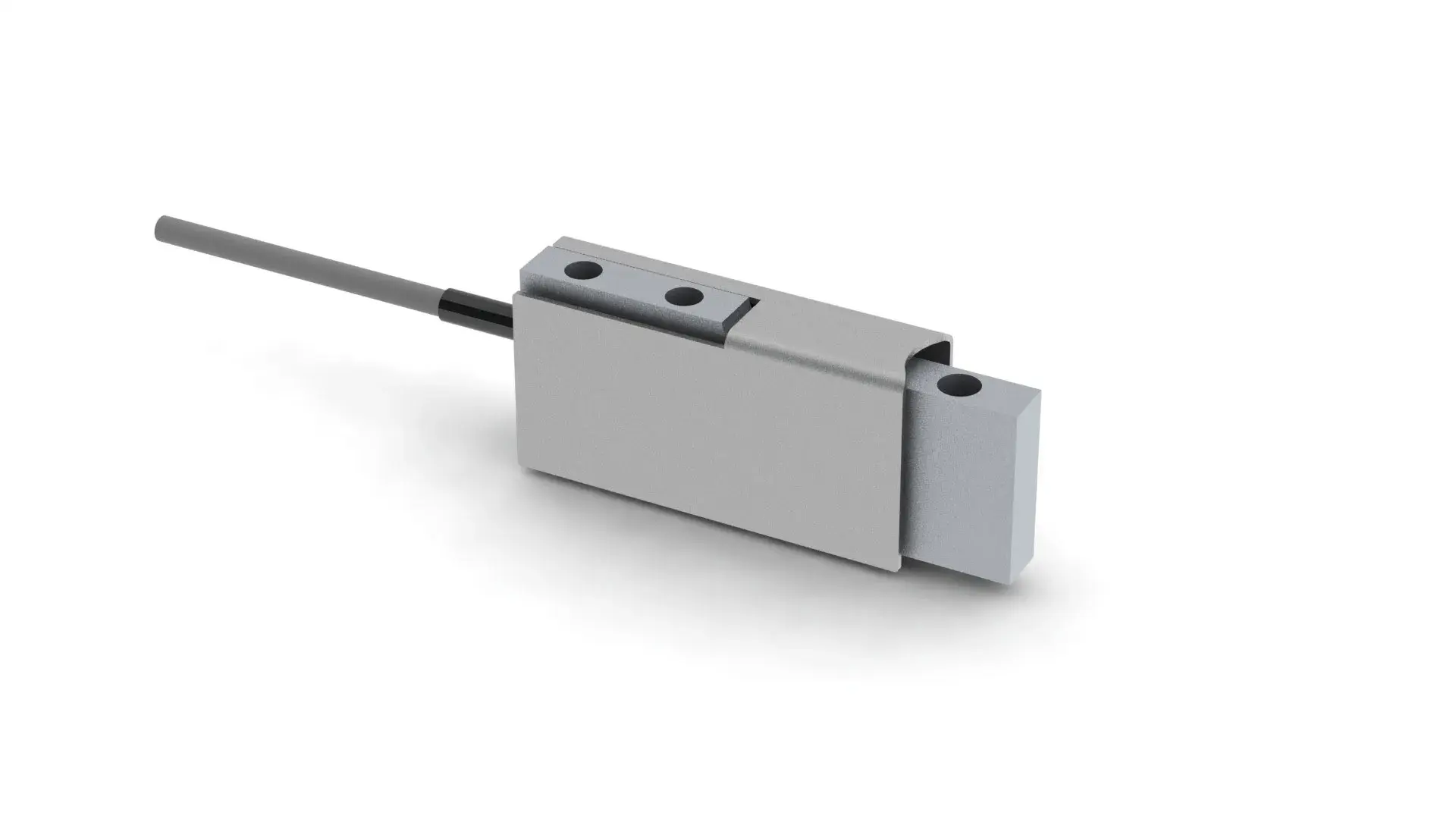
HIGH-PRECISION LOAD CELLS FOR AIRFRAME STRUCTURAL TESTING
Load cells measure forces exerted on the airframe during testing.
These devices are engineered to provide:
- Exceptional Accuracy: High-resolution force measurement ensures reliable test data.
- Overload Protection: Advanced load cells are designed to withstand extreme forces without compromising accuracy.
- Temperature Compensation: Sensors must remain precise across varying temperature ranges, ensuring accurate readings in both low- and high-temperature environments.
- Dual-Channel Redundancy: Some modern load cells include redundant measurement channels to maintain data integrity even in the event of failure.
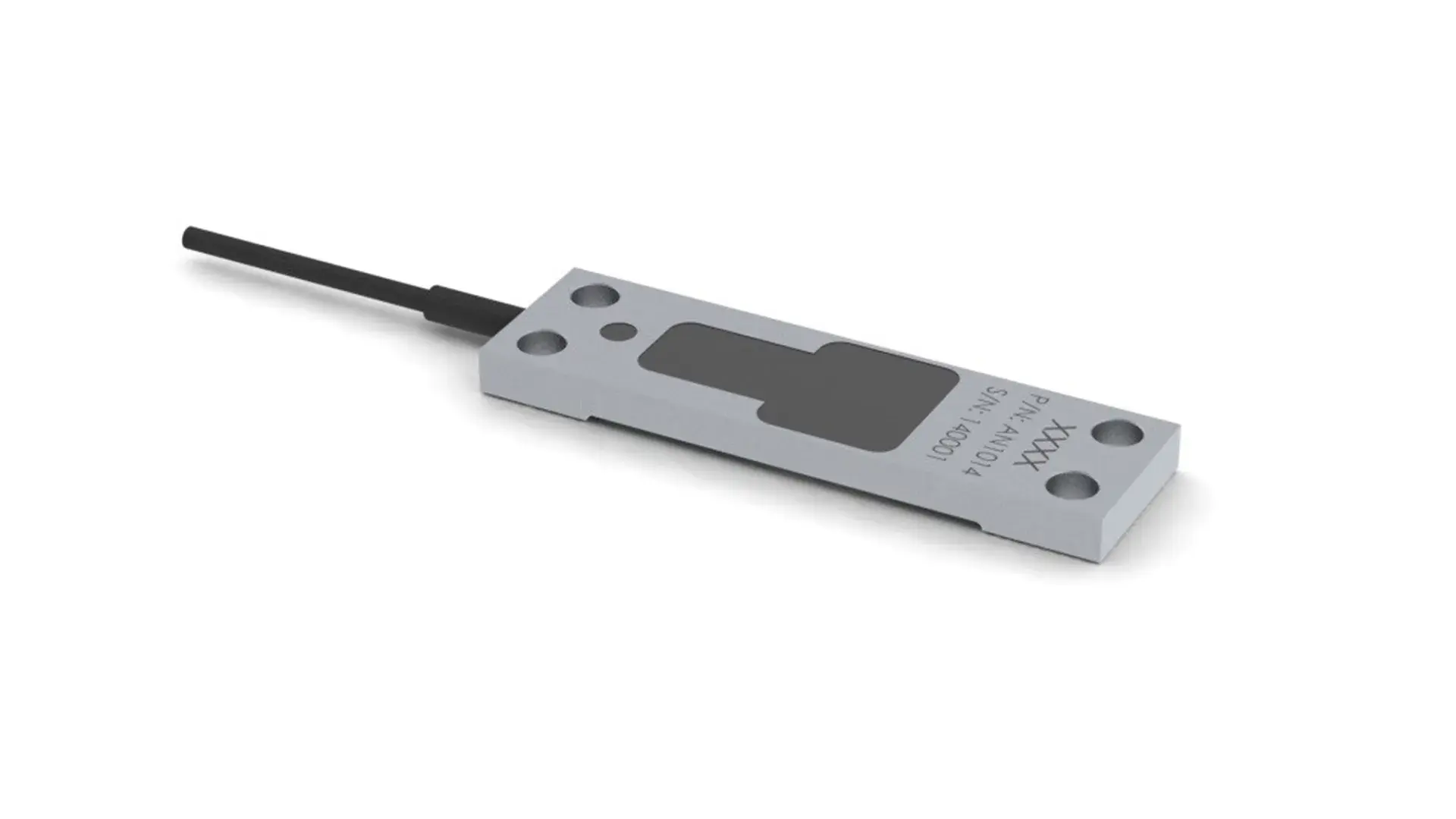
MINIATURE STRAIN GAUGES FOR REAL-TIME STRESS ANALYSIS
Miniature strain gauges are essential for capturing localized stress and strain data in critical airframe components.
These sensors provide:
- Compact, High-Sensitivity Measurements: Ideal for tight, intricate areas where standard sensors cannot be placed.
- Robust Adhesive Bonding Solutions: Proper bonding techniques improve sensor longevity and accuracy.
- Advanced Data Acquisition Systems: Modern testing setups incorporate digital signal processing for real-time stress monitoring and data visualization.
Subscribe for Insights
Industry insights, trends, events and unmissable content straight to your inbox
Sign up to our newsletter to get insider access to stay up to date with all things custom strain gauge sensing
ENHANCING AIRFRAME STRUCTURAL TESTING WITH REAL-TIME DATA ACQUISITION
Modern airframe structural testing incorporates real-time data acquisition systems that allow engineers to monitor stress distribution, crack propagation, and fatigue behavior with high precision.
These systems:
- Integrate with Multiple Sensor Types: Load cells, strain gauges, and temperature sensors work together to provide a complete picture of structural integrity.
- Enable Immediate Adjustments: Engineers can make real-time decisions based on live data, optimizing test procedures and improving accuracy.
- Reduce Testing Time and Costs: Efficient data acquisition reduces downtime and accelerates aircraft certification processes.
WHY HITEC SENSORS IS THE PREFERRED PARTNER FOR AIRFRAME STRUCTURAL TESTING
HITEC Sensors is a leader in aerospace testing solutions, offering industry-specific expertise, advanced sensor technology, and tailored engineering support. Our precision load cells and strain gauges are designed to withstand the most demanding aerospace testing environments, ensuring superior performance and reliability.
Comprehensive Testing Solutions
We provide a one-stop-shop for aerospace structural testing, including custom load cells, strain gauge solutions, and real-time data acquisition systems. Our team of skilled engineers offers consulting and Field support to optimize testing setups.
Unmatched Reliability and Precision
With a 100% quality track record, HITEC Sensors ensures that every product meets the highest industry standards. Our fast lead times and efficient processes help customers meet strict project deadlines without sacrificing accuracy.
Innovative and Cost-Effective Solutions
We offer high-value, cost-effective sensor solutions tailored to the aerospace industry’s evolving needs. Our expertise in temperature compensation and overload protection ensures that our sensors provide accurate, repeatable results even in extreme conditions.
ELEVATE YOUR AIRFRAME STRUCTURAL TESTING WITH HITEC SENSORS
Airframe structural testing is a critical component of aircraft design and certification, requiring highly precise measurement tools, real-time data acquisition, and advanced fatigue analysis. The challenges of testing modern aerospace structures demand cutting-edge sensor technology capable of delivering accurate, reliable results under extreme conditions.
HITEC Sensors provides custom load cells, miniature strain gauges, and expert engineering support to ensure that fuselage testing is conducted with unmatched accuracy and efficiency. Our commitment to innovation and reliability makes us the preferred partner for aerospace structural testing solutions.
For expert support and precision-engineered sensor solutions, contact HITEC Sensors today to discover how we can enhance your fuselage testing capabilities.