Strain gauge technology doesn't come in a one size fits all scenario
The solutions are as diverse and individual as are the applications for which they are specified and developed. HITEC works with customers to either develop bespoke solutions or add their expertise and knowledge to a customer’s design to come up with a more refined and targeted solution.
The decision on when to use a semiconductor strain gauge over the use of a more traditional foil gauge often, but not always, comes down to the need for higher levels of safety. For example, when a customer requires a safety factor of 10:1 ratio of a part under test, the part is required to withstand 10x the load they are looking for without being damaged. In medical applications, where customers are faced with the knowledge that, for example, it takes 8 grams of force to rupture a tissue, it is then calculated that they require equipment and components to withstand a 1lb force. The solution in this scenario is to use semiconductor gauges as they are much more sensitive than regular foil gauges. A semiconductor gauge produces an output signal approximately 75 times greater than a foil strain gauge, which allows for measurement of smaller loads. For example, a load cell with a 2 mV/V output using a foil strain gauge with a typical gauge factor of 2.0 would have a 150 mV/V output using a semiconductor strain gauge with a gauge factor of 150.
Additional requirements in some medical applications include the need for a small form factor when dealing with parts or tools that enter the body. Semiconductor gauges have a much smaller geometry than foil gauges and are ideal in such applications.
HITEC has experience developing sensors with semiconductor strain gauges for medical applications where exacting force measurements are required, such as stents that are used in procedures to ensure functionality of the arteries. Transducerized components and custom designed load cells are effective ways of measuring the forces being exerted on walls of the artery.
A tonometer is a diagnostic tool for measuring intraocular pressure within the eyeball. It is a handheld device shaped like a large pen that incorporates semiconductor strain gauges. Once the compression force is applied to the sclera, a high pressure reading (22 mmHg or more) could show signs of glaucoma.
An innovative company in the prosthetic limb field approached HITEC with an existing design for force feedback on knee joints. Minimal design effort was required on HITEC’s part given the existing design, however our design engineers were called upon to help select proper semiconductor strain gauges as well as devise the temperature compensation techniques required for production units.
Strain gauges can be used to measure forces on minimally invasive surgical instruments. When installed on a trocar for advanced laparoscopic surgery in the abdomen, strain gauges allow force measurement in the X and Y direction for better viewing of the working site, as well as measurement of pressure on both the trocar and the entry site. Two full bending bridges are installed to measure both directions. Optimal combinations of adhesives and protective coatings are selected to accommodate sterilization.
Subscribe for Insights
Industry insights, trends, events and unmissable content straight to your inbox
Sign up to our newsletter to get insider access to stay up to date with all things custom strain gauge sensing
Parameter | Metal Strain Gauge (Foil) | Semiconductor Strain Gauge |
---|---|---|
Measurement Range (µƐ) | 0.1 - 40,000 | 0.001 - 3000 |
Gauge Factor | 2.0 – 4.5 | 50 - 200 |
Resistance (Ω) | 120, 350, 600, ….., 5000 | 1000 - 5000 |
Resistance Tolerance | 0.1% - 0.2% | 1% - 2% |
Size (mm) | 0.4 – 150 (standard 3 – 6) | 1 - 5 |
Table 1 - Comparison of key nominal specification differences between foil based and semiconductor strain gauges
Each application will have its own set of specification requirements which enable the HITEC technical team to identify the most appropriate solution, including advanced safety specifications and exposure to harsh environments or extreme temperatures. HITEC has a proprietary assembly and electrical configuration process designed to work with matched sets of semiconductor gauges and provide temperature compensation, which reduces the variability of the output signal due to temperature effects.
HITEC is flexible in its approach to working with customers and can develop solutions from initial design through volume production, work on creating bespoke solutions or take a customer’s existing design and apply additional expertise to advance the solution. For further details please contact us.
Speak to our experts
Provide us with your information and our team will contact you
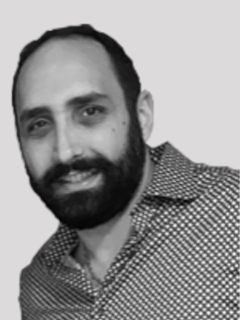
Domenic El-Achkar
Domenic El-Achkar is Director of Engineering for HITEC Sensors. He started with the company in May of 2000, as a Co-Op student while earning his B.S. in Mechanical Engineering at UMass Lowell and later earning his MBA. Domenic has developed his engineering capabilities from applications support through design, test and measurement, management, and departmental leadership. Domenic combines broad technical knowledge with a commercial mindset and good communication skills to be a very effective customer-facing technical leader. He enjoys visiting customers, developing partnerships, innovative sensor designs, and helping customers solve problems.