The rapid growth of wind energy has led to the development of larger and more advanced wind turbine designs. As these turbines become larger, understanding their structural behaviour under various loads becomes increasingly complex.
To address these challenges, HITEC Sensors has developed strain gauge-based sensing solutions and instrumentation that accurately measure and monitor the loads experienced by wind turbine blades during operation.
Strain Gauge Instrumentation for Wind Turbine Blades
Principle of Strain Measurement
Strain gauges are widely used in engineering applications to measure mechanical strain, which is the ratio of deformation to the original length of a material under stress. These gauges consist of a fine wire or foil grid that is bonded to the surface of the structure being monitored. As the structure experiences mechanical loading, the strain gauge experiences strain, leading to changes in its electrical resistance. By measuring these changes in resistance, engineers can accurately determine the strain levels and assess the structural behaviour of the wind turbine blades.
Full-Scale Static Load Measurement
Full-scale static load measurement is a critical aspect of wind turbine design validation. By installing strain gauges on the blades at strategic locations, engineers can gather real-time data on the loads experienced by the blades under various operational conditions. This data enables them to verify the structural integrity of the blades and identify potential areas for improvement in the design.
Design Validation and Certification Requirements
Design Validation Using Strain Gauges
Wind turbine manufacturers subject their designs to rigorous testing to ensure they meet safety standards and perform optimally in various environmental conditions. Strain gauge instrumentation plays a key role in design validation by providing valuable data on the actual loads experienced by the blades during prototype testing. Engineers use this data to validate their design models and make necessary adjustments to ensure the blades' structural integrity and performance.
Compliance with Certification Standards
Certification organizations, such as the International Electrotechnical Commission (IEC), set stringent standards for wind turbine design, performance, and safety. Full-scale static load measurement using strain gauges is crucial to meet these certification requirements. The data obtained from the instrumentation is essential to demonstrate that the wind turbine blades can withstand the expected loads over their intended lifespan.
Subscribe for Insights
Industry insights, trends, events and unmissable content straight to your inbox
Sign up to our newsletter to get insider access to stay up to date with all things custom strain gauge sensing
Fatigue Testing and Cycle Loading
Fatigue Testing with Strain Gauges
In addition to full-scale static load measurement, strain gauges also play a pivotal role in fatigue testing of wind turbine blades. Fatigue is the process of material degradation and damage accumulation under cyclic loading conditions, which is a common occurrence during wind turbine operation. Strain gauges are installed to monitor the cyclic loading and determine the fatigue life of the blades. This information is crucial for optimizing the blade design, predicting maintenance requirements, and ensuring the long-term reliability of the turbine.
Enhanced Wind Turbine Performance and Safety
By providing accurate data on the fatigue behavior of the blades, strain gauge instrumentation contributes significantly to enhancing wind turbine performance and safety. Understanding the fatigue characteristics allows manufacturers to design blades with improved durability, reducing the risk of structural failure and unplanned downtime.
Strain Gauge Instrumentation Services
HITEC offers specialized strain gauge instrumentation services tailored to the<br>unique needs of wind turbine manufacturers
Our experienced team of engineers and technicians are equipped to install strain gauges on wind turbine blades efficiently and accurately. HITEC provides services both in-house and on-location, ensuring that the installation and data collection process is seamless and reliable.
Conclusion
Strain gauge instrumentation plays a vital role in full-scale static load measurement for wind turbine blades. By employing HITEC sensors, engineers can ensure the structural integrity, design validation, and certification compliance of wind turbines, enhancing their performance and safety. The accurate data obtained through strain gauges also enables optimized fatigue testing, leading to more durable and reliable wind turbine designs, thus advancing the growth of clean and sustainable wind energy.
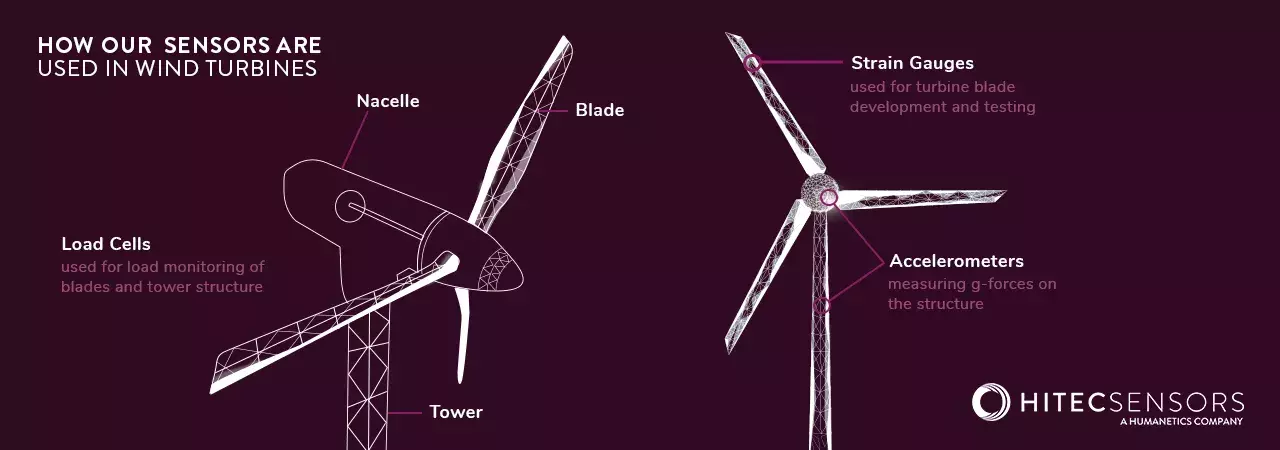
Speak to our experts
Provide us with your information and our team will contact you
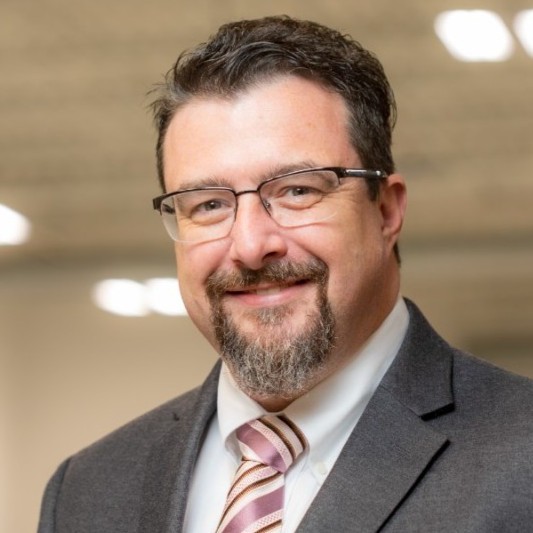
Jeff Drecnik
Jeff Drecnik serves as the Director of Sales at HITEC Sensors, where he brings extensive expertise in driving business growth and fostering strategic partnerships. With a proven track record spanning over 30 years in sales roles, Jeff is instrumental in guiding HITEC Sensors' sales initiatives to new heights. Drawing on his in-depth knowledge of custom strain gauge solutions, Jeff excels in crafting tailored results that address clients' unique challenges.