The standards and regulations surrounding aerospace applications are extensive, but adherence to the requirements is critical and in many cases mandatory. In relation to force sensing for in-flight applications, the key areas are, but are not limited to, Design, Manufacturing, Social and Environmental.
DESIGN
For mechanical design analysis, the key factors are the strength of the materials involved, with appropriate adjustment for the grades of material and the effects of processing. It is imperative that the design data is not arbitrary and not based on an individual manufacturer’s data sheet or other piece of information that exists outside of the universal standard, which is the MMPDS handbook. This defines the data to be used for the stress analysis, vibration analysis and thermal analysis that must be performed before presenting a design to a customer for review.
The design process must also take account of the MIL specifications and Aerospace Recommended Practices (ARPs) of which the variations are extensive. Costs associated with these specifications also have to be considered as although previously they have been free of charge, they now generally have to be paid for. This means that each time a customer specifies something new, another standard will have to be purchased, evaluated, complied-with and kept up to date.
From an electronics perspective, the key analysis document is the Electronics Design Justification, which takes guidance from RTCA DO-254 which introduces the concept of Design Assurance Levels. Each type of application is rated at a particular Design Assurance Level (DAL) where Level A covers the most critical applications such as flight control, through to Level E which covers those that are less critical, such as in-flight entertainment. The level of a particular application determines the way in which it is regulated, and it is highly important to define this at the start of the programme as it will make a big difference in terms of the amount of work that has to be done on the justification and verification.
The analyses for safety are obviously very important and must include the structural safety, the failure modes effects and criticality analysis, and the reliability prediction, brought together to form the subsystem hazard analysis. Given that reliability and the thermal environment are closely related, the higher the average temperature, the more difficult it is to achieve high reliability numbers, therefore managing the thermal environment and minimising heat dissipation is vital.
The electromagnetic compatibility, typically referred to as EMC but also known as EMI or E3, provides a further set of specifications which can vary significantly, depending on whether the application is civil or military. We typically design to ADS-37 or MIL-464, which provides a level of capability over and above that of most civil applications. However, cost has to be considered as the solutions required for the most severe environments come at high expense. There is no need to implement the highest standards for a sensor that will be buried internally, deep within the aircraft, compared to one that is mounted externally, which will most likely be subjected to a much more severe electromagnetic environment. The requirements for EMC are evaluated to ensure that the expenses are in proportion to the environment the sensor will be exposed to.
Further environmental standards are specified by the well-known RTCA DO-160, which covers a multitude of factors including temperature, humidity and altitude, and explains the procedures for testing for these in detail. For military applications, MIL-STD-810 would be the required standard, covering a similar but different set of factors. Typically, a combination of both sets of standards would be used when considering new applications.
MANUFACTURING
The AS9100 series can be considered as the gold standard for regulation and control of variability within manufacturing in the aerospace industry. Also in use is the J-STD-001, which relates to acceptance within process, and J-STD-001ES if the application is related to space, which is an area that HITEC is already qualified and equipped for. The requirements for the inspection and acceptance during the build are provided by the relevant MIL standards along with IPC-610 and 620.
Traceability is hugely important within all realms of manufacturing for aerospace as every material item used must be fully traceable right back to the original point of creation. This can often be a challenging area, particularly if a material item has come from distribution as it can be difficult to fully trace it back and maintain the full chain of custody. For example, even for something as simple as a lock nut, its path must be fully traced back through every distributor that has handled it. In addition to this, the certificates of each material and the processes it was subjected to must also be readily accessible and traceable throughout the chain of custody, which makes this a significant and time-consuming area of work.
Once a product has been designed and submitted for qualification, the process is fixed from this point onwards, which is why it is imperative that every effort is made to perfect it from the start as there will be no further opportunity to amend it. This is particularly significant for processes that are more advanced or more difficult to carry out, as once this is fixed, this is the process that will need to be followed for as long as it is in use. In terms of acceptance testing, this is something that would be agreed with the customer beforehand using to determine what needs to be tested and how, along with specifying what kinds of load applications are involved. This could include special fixtures or customer parts that will be involved in applying the respective loads in the airframe. Once the product has been reviewed and accepted, it will receive a certificate of conformity, which in the case of airworthiness requirements, would be an FAA 8130 tag or EASA Form 1, which then allows for the product to be released.
Subscribe for Insights
Industry insights, trends, events and unmissable content straight to your inbox
Sign up to our newsletter to get insider access to stay up to date with all things custom strain gauge sensing
SOCIAL & ENVIRONMENTAL
Social and environmental regulations are growing in significance within the aerospace industry and their implications are now having a profound impact on the components and materials that can be used due to changing standards. Many of the parts that have been proven in common use over many years no longer comply with new environmental standards because they contain a component or chemical that is on the undesirable list. This creates a new area of work in finding a functionally equivalent alternative which can be qualified and verified against the new environmental standards while performing as well or better than the original legacy part. In order to manage this for the lifetime of the product, we focus on limiting obsolescence risks in the design and specification stage by choosing materials and processes that are unlikely to become obsolete in the foreseeable future.
Further social and corporate responsibilities include ensuring the same standards are in place across all sectors of the manufacturing chain. For example, if a company such as HITEC has a standard in place that means they do not use conflict materials, the complete chain of subcontractors and suppliers for that company must also be aware of and comply with that standard, including the original raw material companies that extract the materials. Ensuring that all of these standards are in place throughout the supply chain is the responsibility of the company as they must know where all their materials have come from and how they have been handled. Decarbonisation must also be considered in the same way, taking steps to reduce the carbon footprint of the company and the supply chain as a whole.
In summary, the specifications and standards for design and manufacturing within the aerospace industry have very stringent implications which are outlined in the respective guides such as the RTCA DO-160, DO-254, J-STD-001 and the EMC standards such as ADS-37. To summarise some of the most important areas, it is key that the design and manufacturing process are developed and perfected before being submitted for verification due to the fixed process which restricts any opportunity to make changes further down the line. Furthermore, the compliance with standards and regulations throughout the entire supply chain of a company must be ensured, which is particularly important due to growing environmental concerns, which will soon prohibit the use of certain parts, components and processes.
Speak to our experts
Provide us with your information and our team will contact you
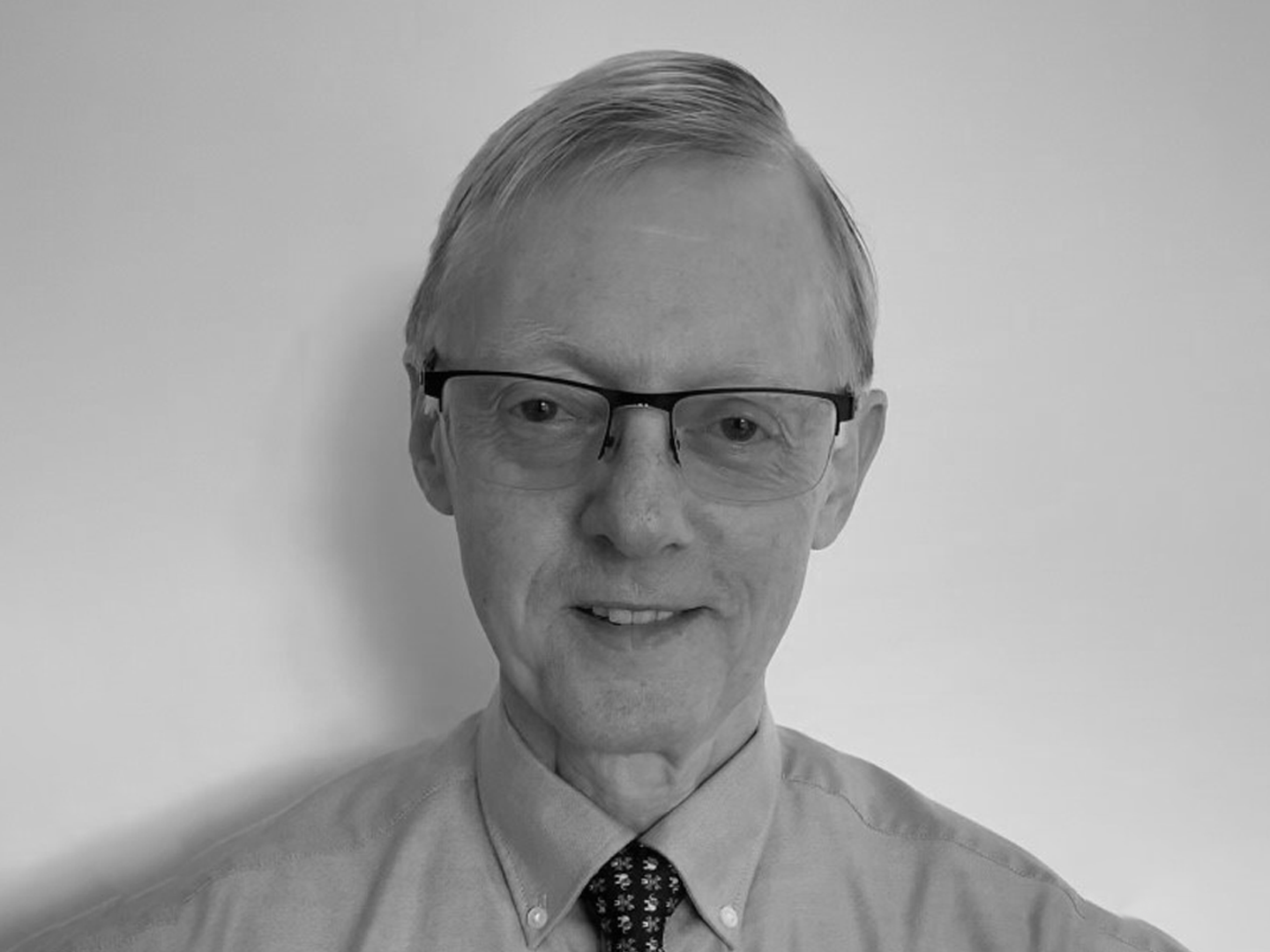
Andy Royal
After accumulating 30 years of experience in managing technical businesses on three continents, Andy turned his attention to the specialized and challenging opportunities for aerospace in-flight force and torque sensing and was a founder member of the 2009 start-up, Aero Sense Technologies. Andy stayed with the company after its 2018 acquisition by HITEC Sensors and ensured a smooth transition with continued blue-chip customer satisfaction. Andy continues to be involved with new aerospace sensing opportunities for flight controls, flight safety systems and aircraft capability upgrades.