How do Strain Gauges Work?
The concept of a strain gauge is fairly simple in theory and can be explained in terms of a strain sensitive resistor, which is the basic principle upon which a strain gauge operates. A simple example would be a length of wire which upon being stretched would become thinner and increase its resistance. Similarly, if that wire was to be compressed, its cross-section would become larger and its resistance would reduce. A strain gauge builds upon this principle and is a resistor that is formed from a thin foil layer which can be attached to a structure to measure the strain underneath it.
It is known from Hooke’s law that strain is a function of stress, therefore if a strain gauge is applied to any structure subjected to stress, the resulting strain can be measured with the strain gauge. For example, a strain gauge can be attached to an airframe to measure stresses during flight or in the case of a force transducer, the strain gauge can be mounted on a specially-designed structure that directs the stresses and strains in a more ideal way, therefore enabling the accuracy to be increased.
To improve the accuracy of strain gauge sensing, four strain gauges are typically connected together into a Wheatstone bridge configuration. The reason for this is to convert the measurement from resistance to voltage, as measuring change in resistance is very difficult to do accurately and is subject to numerous external influences. The bridge arrangement allows greater accuracy and reduces the influences from external factors such as changes in temperature.
What are the key factors involved?
Strain gauges can be mounted directly on the structure that is being monitored and this would be the typical case for an airframe stress test. Force and torque sensors tend to be mounted directly in the load path at a convenient point. This means that the forces generated, for example by an actuator of some kind, would pass directly through the force or torque sensor. In either case, it is vital that the loads are analysed to ensure that the safety factors necessary for an airframe application are being complied with.
The three load types that need to be considered are the working load, the limit load and the ultimate load, as these are the main cost and design drivers. The working load refers to the typical load that is expected to be carried by the sensor, and this can be in any unit such as Newtons, pounds, Newton-meters, which is then calibrated against the output of the sensor. However, if it is possible for an increased load to occur that is beyond the normal working load, then this is known as the limit load.
This limit load must be carried by the sensor without causing any degradation and when removed, the sensor must return to normal operation within its specified accuracy. If, for example, a sensor is carrying a normal working load of 1000 Newtons in tension or compression, with the typical factor of multiplication for limit loads being around 1.5, this same sensor could accommodate a load of 1500 Newtons. The challenge this presents is that the sensor may have to go back through zero in the opposite direction to minus 1500 Newtons and when that force is released, it must come back to its original measured value and continue to operate within the accuracy specifications that were stated for the working load. It is crucial that all performance parameters are maintained, including such cases of a reversing limit load.
The factor of safety at limit load must be equal to or greater than 1.5 at all times to ensure that worst case scenarios will remain within safety parameters. This is because the ultimate load, which is the load at which the sensor has to maintain its integrity but not necessarily its function, is typically 1.5 times the limit load, thus ensuring that the Factor of Safety is always equal to or greater than one in the worst case temperature and environment at ultimate load.
Consequently, these three parameters are key when making decisions about the shape and size of the force sensor. For example, when converting an existing hydraulic actuation system to an electric actuator where the force sensor is to be built into the structure of the actuator, these three factors must be considered to determine the physical size of the sensor and the options available in terms of its design.
Other key factors include accuracy and environment, which very often go together. In an instance where a sensor for a particular application demonstrates an accuracy in the calibration laboratory of say 0.1 percent, this performance would have to be demonstrated over the complete environment, not just at a stable room temperature before it can be regarded as an appropriate solution. Within the extensive range of environments that exist for aerospace applications, accuracy must be maintained throughout variations of temperature, altitude, humidity, icing, vibration, fluids exposure and electromagnetic effects.
This means that overall accuracy for force sensors tends to sit in the range of 1 to 3 percent, depending on the type of sensor, because this performance has to be achieved over the entire environment. This must also apply throughout the life of the sensor, typically between 25 to 30 years, but 40 years in some applications. Typically, there will be no way to adjust or recalibrate the sensor when it is in service, so it has to be accurate for the specified lifetime in the specified environment.
What evidence do we have?
Specifically referring to in-flight applications, there are a number of examples of how force sensors are replacing more traditional technology in order to provide solutions to various challenges within the aerospace industry. One example is the replacement of hydraulic actuation with electric actuation within the ‘more electric’ aircraft, which has helped to reduce both weight and cost. This involves the replacing of traditional, hydraulically powered force actuators, which used pressure sensors, with electric actuators and various other kinds of electromechanical devices, which employ force sensors in place of pressure sensors to give force feedback. An example of this would be the Airbus A220 which uses an electric braking actuator system with force sensing feedback. As we move forward to the all-electric aircraft, we are seeing a significant increase in applicability for force feedback sensors in electric actuators, as having a hydraulic system on an all-electric aircraft can present quite a burden. This explains the trend towards all-electric systems.
Another area in which force sensors have been applied is in flight controls, such as the control column, yoke or stick, which have traditionally been fitted with springs and position sensors to determine the pilot’s input forces. There have been considerable advancements in this application area because force sensors offer a high stiffness solution, which in turn allows progression towards the active stick solution. This means that the pilot does not move the stick itself, but rather applies a force to the stick which then moves as a result of the force sensor detecting the applied force and the control system commanding an actuator to move the stick. The flight control system then allows force feedback to the pilot according to the phase of flight. For example, at low speeds, the stick would have fairly low stiffness and as the airspeed increases, that stiffness increases also and this can be programmed to have both hard stops and soft stops, making this a very flexible approach where both pilots know what the other is doing, given that the sticks are linked. As this is a flight critical application requiring quad redundancy, an eight-channel force sensor would be used in this case.
Subscribe for Insights
Industry insights, trends, events and unmissable content straight to your inbox
Sign up to our newsletter to get insider access to stay up to date with all things custom strain gauge sensing
What is the significance of miniaturisation?
The significant reduction in the physical size of sensors packages has come about because of advancements in two crucial areas, namely strain gauges and electronics. Strain gauge production techniques based on laser trimming have undergone considerable enhancement to the point where it is now possible to use certain strain gauge types, such as full bridge types, which were previously unusable due to difficulties in terms of size and cost. However, now that these are fully miniaturised, these challenges have been overcome.
The miniaturisation of electronic components has also presented solutions in terms of amplification which, due to the low-level signals provided by strain gauges, is almost always required to get the signal to the host. Thus, electronic miniaturisation has made it far easier to put electronics in with the sensor and achieve a doubling of the functionality in a much smaller package.
However, to continue complying with the factor of safety as mentioned earlier, the laws of physics have to be respected. The loads to be carried have to be considered and the sensors carrying those respective loads must be sized appropriately so they remain within those safety parameters. An example would be a weight-on-wheels sensor within the undercarriage, which is obviously a application that sees significant forces.
How does interfacing work?
The interfacing is the way in which we transfer the signals provided by the force sensor to the aircraft subsystems. As explained previously, the very low-level signals typical of strain gauges need to be amplified in order to be of use to the aircraft subsystems and the traditional way in which this works is by routing the output through specialised amplifiers that have to be installed somewhere within the airframe.
However, it is now possible to integrate the amplifier within the force sensor in order to provide an output format that the subsystem can already cope with, namely the pre-existing standard voltage sensing or current sensing capability. Regardless of the configuration, the calibration is always performed during the build and is fixed for the lifetime of the sensor.
There are cases where alternative formats with different configurations may be required, but voltage sensing remains the most common form of interface for sensors within the pressurised zone. For example, in the cockpit area, short cables can be run from sensors into flight control systems or flight data recorders. Voltage outputs such can be bipolar, for example plus or minus four volts, which would be an output format to choose when high accuracy is required. In other cases, a unipolar format centred on a different voltage could be used, with the potential for a simpler configuration which can result in the reduction in the number of wires and a corresponding reduction in weight, examples being 5 plus or minus 4 volts, or 4 plus or minus 2.5 volts.
When considering applications outside of the pressurised zone, isolation becomes a crucial factor to ensure that the internal systems are protected from any external influences. This means that any sensors mounted outside the airframe are often run through current loops for ease of isolation. A current amplifier is used to modulate the current in the external loop, which is in turn detected by the internal subsystem. This is well suited to long cable lengths and can be used with a two-wire current loop, which reduces the number of wires. For example, a cable that is 20 metres long would provide a significant saving in terms of weight and cost if only 2 wires were used, with that reduced weight giving benefits throughout the lifetime of the aircraft.
Interfacing force sensors directly to a digital data bus such as ARINC-429 or ARINC-629 is less common, but a concept known as the pseudo-digital output is sometimes used whereby a current loop output is modulated in a digital format, which is far easier for the downstream systems to handle given that the output has already been converted into a binary format. For example, a digital value of ‘zero’ might be represented as four milliamps and a digital value of ‘one’ as twelve milliamps. Thus, using digitalisation in this way is another option for interfacing, which also has significant benefits in terms of ease of isolation.
Speak to our experts
Provide us with your information and our team will contact you
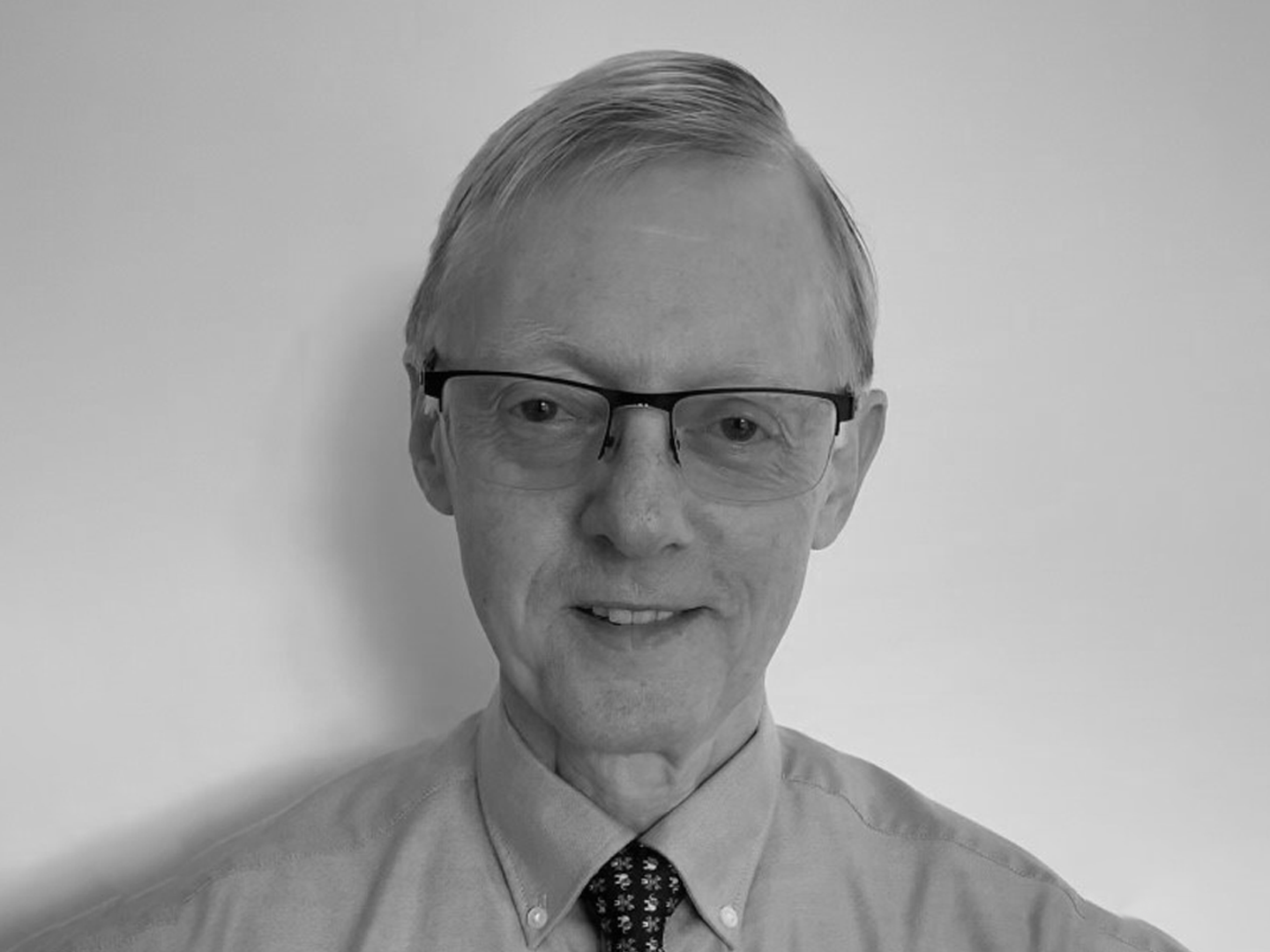
Andy Royal
After accumulating 30 years of experience in managing technical businesses on three continents, Andy turned his attention to the specialized and challenging opportunities for aerospace in-flight force and torque sensing and was a founder member of the 2009 start-up, Aero Sense Technologies. Andy stayed with the company after its 2018 acquisition by HITEC Sensors and ensured a smooth transition with continued blue-chip customer satisfaction. Andy continues to be involved with new aerospace sensing opportunities for flight controls, flight safety systems and aircraft capability upgrades.