What are Assembly Tools?
Assembly tools, such as DC Electric Nutrunners, are commonly used within large scale production lines within advanced manufacturing industries such as automotive, construction, aerospace and other industrial applications to install fasteners (nuts and bolts) onto the piece of machinery being produced such as cars or even aeroplanes.
What sets an assembly tool apart from a more basic manual tool such as a wrench (spanner) is that an assembly tool has in-built force sensing technology and can provide a specific amount of torque depending on the required task. This is critical in many manufacturing sectors as certain fasteners are required to be tightened to an exact value in order to adhere to technical and quality specifications as well as health and safety regulations.
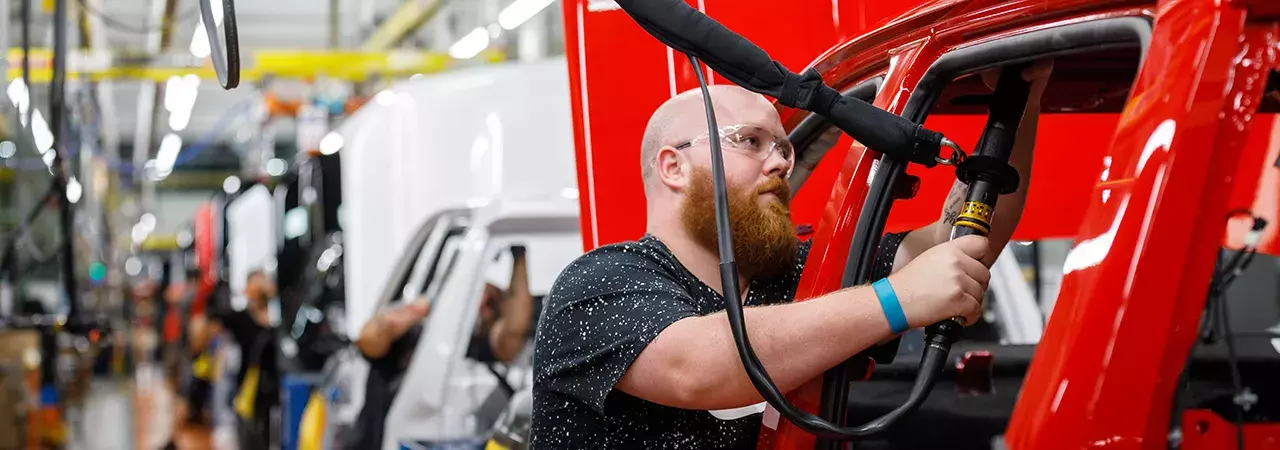
Where Are Assembly Tools Used?
Assembly tools are used across the globe for a wealth of applications from large scale industrial construction projects, within automotive and aerospace production lines all the way to concert stage rigging. These tools can be used by both humans or even robots to improve processing time.
- Assembly/production lines
- Automation
- Advanced manufacturing industries
- Robotics
- Fastening applications
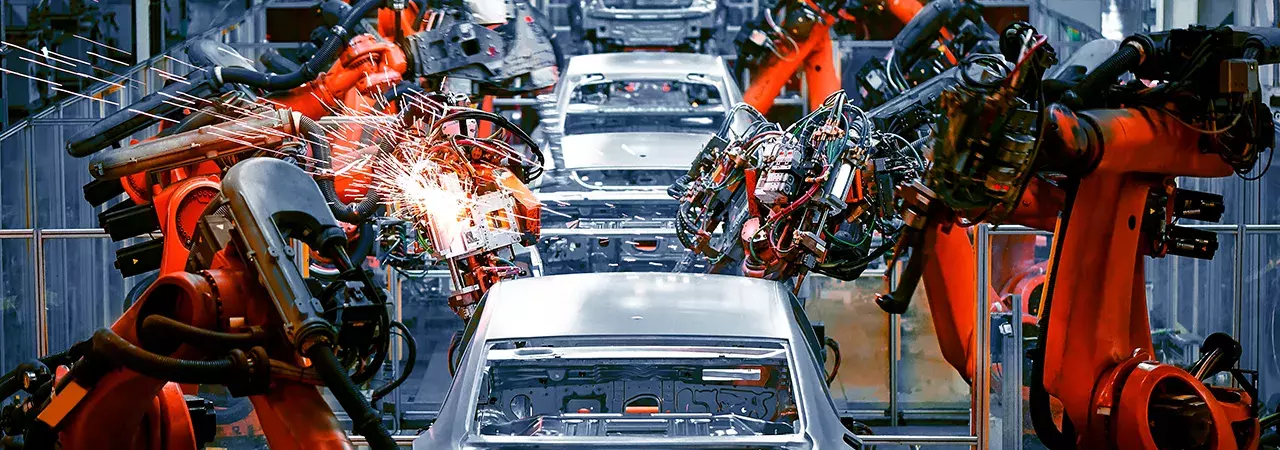
Why Are Custom Sensors Important to Assembly Tools?
Accuracy
Power tools from global manufacturers implement strain gauge sensors into portable products such as drills, electric screwdrivers, and wrenches. Strain gauge-based sensors help provide manufacturers products with accurate force readings including load, torque, pressure, and displacement. Strain gauge transducers provide one of the most accurate ways to measure forces and effectively add sensing capabilities to just about any component or system. Sensors can be integrated into assembly tools at any stage, even during post-production, so existing products can be upgraded to include force sensors.
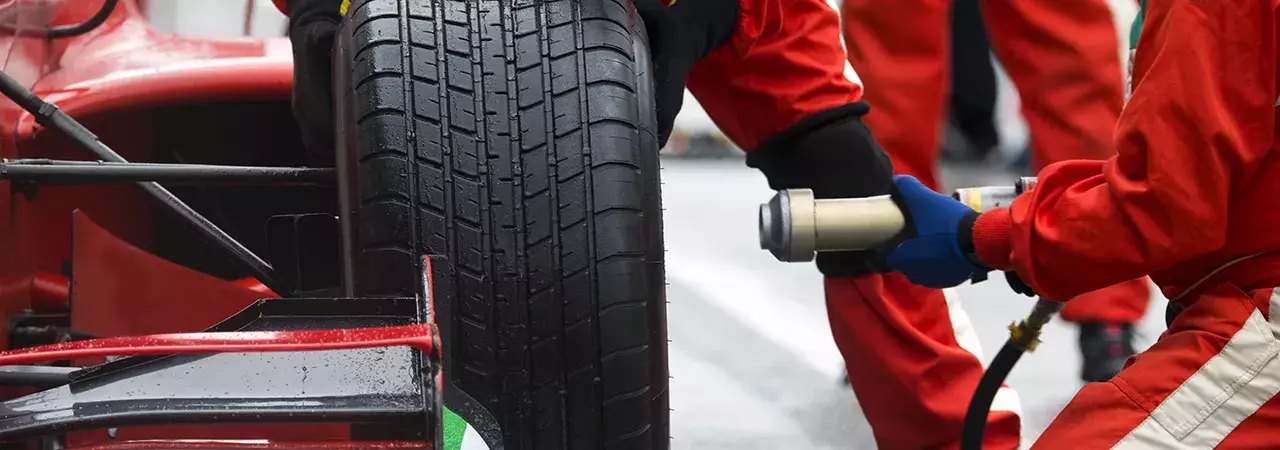
Data Traceability
As well as adjusting and controlling torque, assembly tools can also record the data produced in the fastening process with the help of a more sophisticated force sensor. Modern sensors in assembly tools help provide strict quality control for everything from how tight a component was fastened, to where in the production process it was produced.
The data is stored for accurate traceability of the process. Consistency and quality control are critical in automated assembly lines and without the ability to record manufacturing process data in the event of a line stop, there could be costly and time-consuming delays.
Built-in sensors within the assembly tools can provide the information needed to prevent wide spread delays by accurately and reliably identifying torque values and other factors.
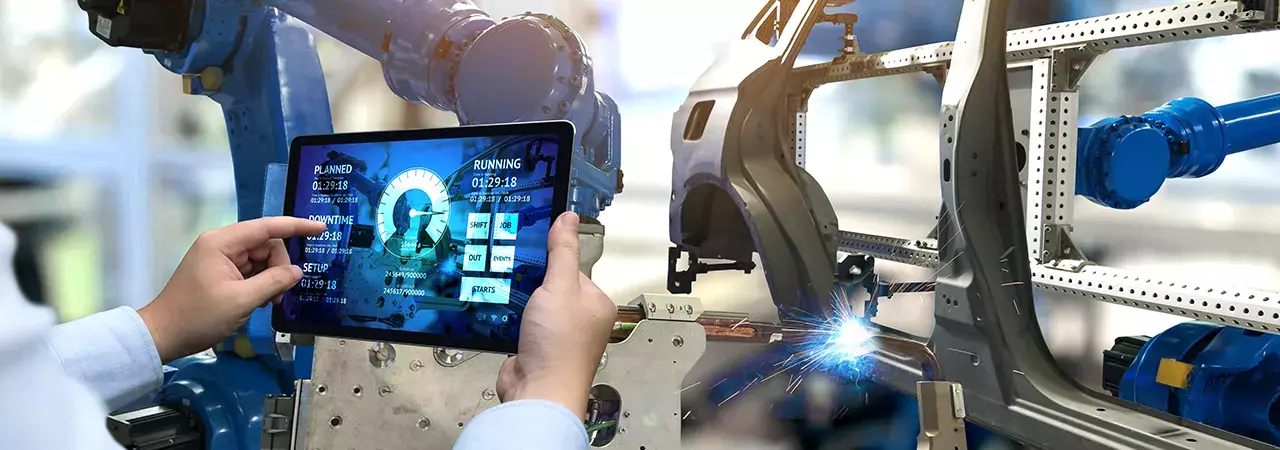
Subscribe for Insights
Industry insights, trends, events and unmissable content straight to your inbox
Sign up to our newsletter to get insider access to stay up to date with all things custom strain gauge sensing
The Importance of Choosing the Right Tool
Some assembly tools utilize a reaction torque sensor that doesn’t spin and converts a torque measurement into an electrical reading. Some use rotary sensors, which have a freely rotating shaft that spins within a fixed housing to measure the torque and resistance produced by the object being measured. This choice depends on the design and purpose of the tool. A sensor can be made with various torque ratings, from very low to extremely high capacity, depending on what it is the customer is assembling. The variety of specific sensors available at HITEC and the customizability on offer allow customers to get the perfect match for their project.
The importance of selecting the correct sensor cannot be understated as it ensures components are set at the correct torque settings to optimize performance and durability. In the worst case, bolts can vibrate and come loose due to insufficient torque, causing damage to components and posing obvious safety risks, especially when referring to the automotive industry. On the other hand, when too much torque is applied to a bolt, it can shear, wasting both materials and production time for the manufacturer. It may also damage the threading of the bolt, resulting in increased component fatigue and early faults.
What Can HITEC Offer?
At HITEC Sensors, we offer a wide range of torque sensors designed for, amongst other industrial applications, advanced assembly tools. Our diverse range of solutions for assembly tools applications, include OEM sensors that are embedded in power tools to measure and control critical assembly processes through to sensors that calculate the performance of powertrains in large off-road construction equipment.
If your application requires a little more consideration, we ‘ll be happy to modify an existing sensor or do a custom design to meeting your application requirements.
Often we design and manufacture a sensor from concept through to production based upon the customers specific requirements.
Why Choose HITEC?
With over 50 years’ experience in force measurement and sensor design, as well as our world leading team of engineers, HITEC offers;
- Longevity, expertise and global support
- Standard and bespoke torque sensors
- Installation support and calibration
- Our standard products are suitable for use with torque loads ranging from 25 to 7000 ft-lbs with further range possible with customization
- Excellent hysteresis of 0.1 % of the full scale capacity
- Robust and accurate strain gauge sensor design
- Solutions for harsh operating conditions
Our process of creating custom sensors starts with an in-depth analysis of your application/project with our team of application engineers. Using advanced modelling software our team create a design that meets the exact performance requirements of the customer. After the initial ideas have been reviewed and approved, it is then time to create the prototype for qualification testing and once a customer is satisfied with the product, the design is then transferred to OEM production. It’s that easy!
Working closely with our customers allows us to create the most suitable solutions as precisely as possible, whether your application is a one-off project or a large-scale repeatable order, we are here to help!
Speak to our experts
Provide us with your information and our team will contact you
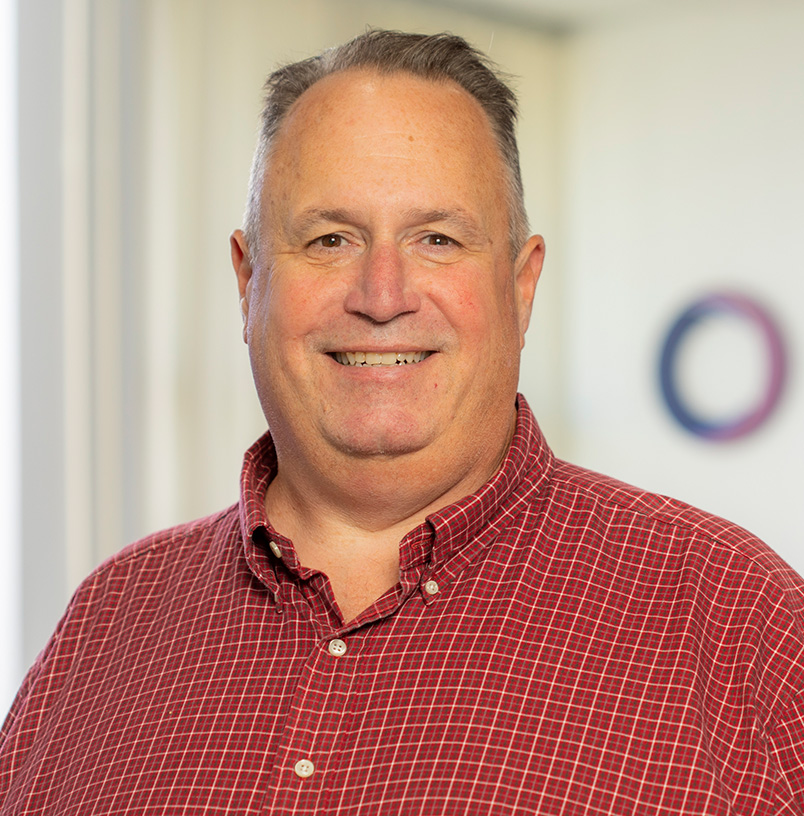
Chris Delling
Chris Delling is Field Sales Manager at HITEC Sensors with expertise in strain-gauge based force and torque sensors. With over 35 years experience in the field as well as industry experience in the construction and agriculture markets, Chris has a passion for sensor design and developing custom solutions.