What is an infusion pump?
Infusion pumps are medical devices used to pump controlled amounts of fluid such as insulin and antibiotics around the body of the patient. There are of two types, one is for stationary purposes and the other is for portable purposes.
Infusion pumps are widely used over manual injection because of how they can supply controlled amounts of fluid with precise accuracy, volume, and interval. They can also be automated to supply fluid at an exact time in specified amounts.
They are commonly used in intensive care units in hospitals as well as nursing homes. They can also be used at home for patients that need around-the-clock assistance. The medical industry is the leading market for infusion pumps due to the treatment of diabetes, chemotherapy, and pain management.
The market is ever-growing due to the prevalence rate of chronic diseases and the advantages infusion pumps offer over traditional pumps. It’s divided into seven key locations based on geographic regions: North America, South America, Eastern Europe, Western Europe, Asia Pacific excluding Japan, Japan, and the Middle East and Africa. North America dominates the market with the Asia Pacific coming in second. Europe is also a strong market for infusion pumps.
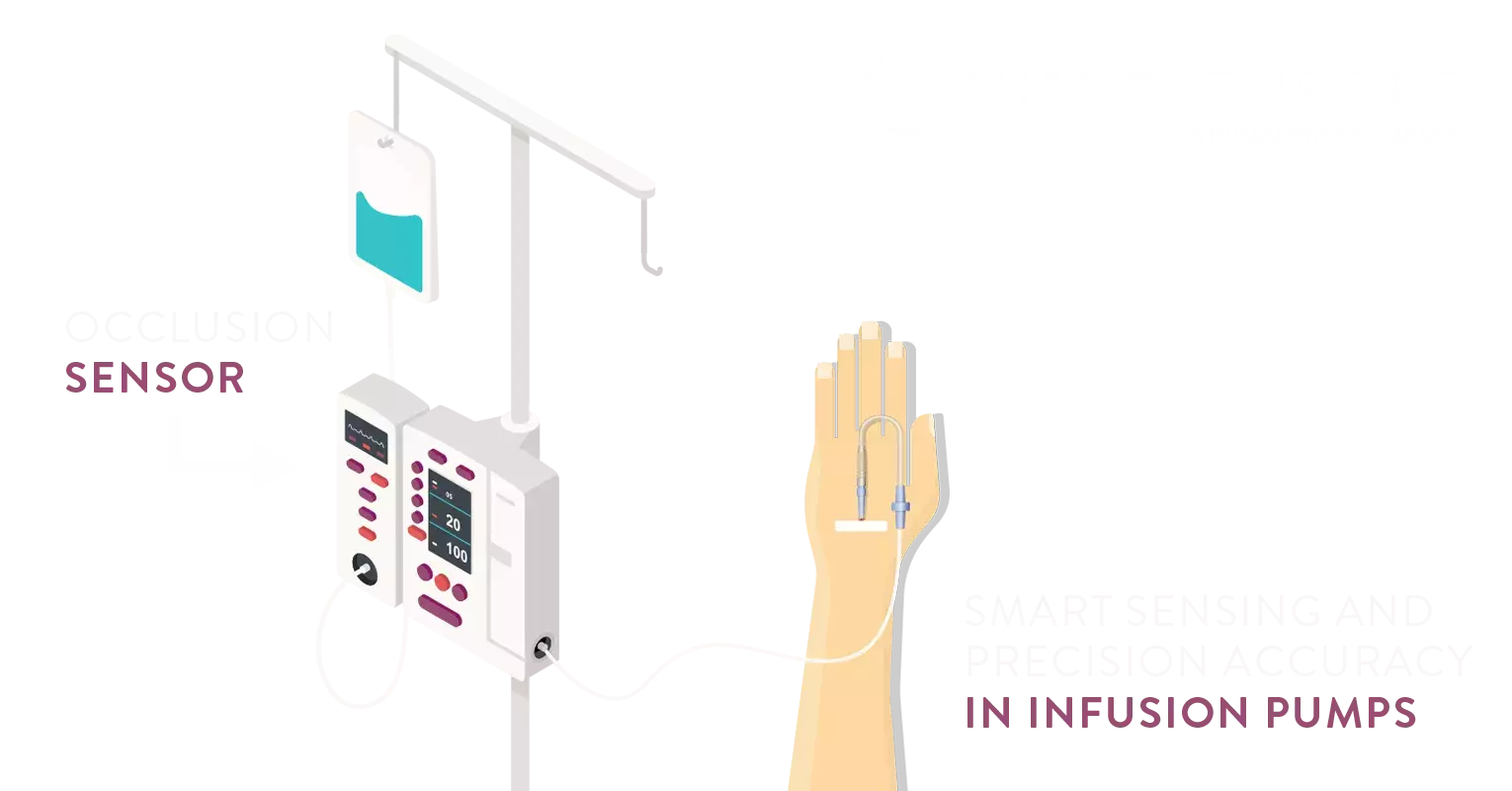
How are force sensors used?
The implementation of force sensors in infusion pumps helps regulate fluid delivery to a patient. The sensors can measure changes in force and send this information to the doctor/clinician to adjust. For example, specific insulin systems monitor the glucose levels in the blood and deliver timely insulin doses to patients with diabetes, while other types of sensors assist in regulating the amount of medication given to a patient.
As well as regulation and dosage, force sensors can also detect possible occlusions and blockages via pressure changes in the tubing of peristaltic infusion pumps. The mechanics of this are simple yet extremely effective. Fluid flows through the tubing, pushing outward and therefore applying force to the sensor. In the case of occlusion, the pressure inside the tubing will change, resulting in a change to the force being applied, indicating an obstruction and notifying the clinician/patient that there is a problem with the fluid path. This allows the correct actions to be taken to avoid any detrimental injuries and complications.
Subscribe for Insights
Industry insights, trends, events and unmissable content straight to your inbox
Sign up to our newsletter to get insider access to stay up to date with all things custom strain gauge sensing
What are the design considerations?
When designing a force sensor for a medical device, it is crucial to consider the sensor's size, durability, and reliability, especially when dealing with critical fluids that could hinder a patient’s health. It is also important to consider the material type and whether the sensor needs to be rigid or flexible to sustain performance in a specified environment. A hermetic seal is crucial, as although strain gauge sensors operate at a very low voltage, if the electrical components of a sensor are exposed to the wrong environment i.e., excessive fluid or extreme temperatures it could cause grounding and drifts. To avoid this, the sensor must have the correct coating applied and be hermetically sealed.
HITEC expertise with sensors
With over 50 years of experience in custom-sensing solutions accompanied by their exhaustive library of application designs, one-offs and high-volume productions, HITEC are one of the leading experts in the Sensor industry and we aim to provide the best possible solution to every application we work on. Medical advancements are becoming more necessary by the day and sensing technology is at the forefront of helping the medical industry reach new standards of reliability and safety.
HITEC are involved in a diverse selection of key industries including: Aerospace, Automotive, Biomedical, Oil, and Energy. HITEC's depth of expertise and involvement in Biomedical is a key factor as to why we are trusted to implant our sensors into medical technology.
Features and Benefits
We provide extremely sensitive strain gauge-based sensors for medical equipment, incorporating a choice of foil and semiconductor technology. Both types have wide applications in the healthcare environment, from precisely measuring larger forces in equipment such as patient tables and imaging systems to the tiny forces involved in the most delicate medical procedures.
Our unique semiconductor strain gauges provide exceptional resolution at the thin and small sizes needed for endoscopic tools, catheters, suture devices, infusion pumps, surgical staplers, and more. We also provide wireless sensors for use in a wide range of applications, such as measuring torque in the rotational components of surgical robots, CT scanners and other medical devices.
When installed on infusion pumps our sensors provide many benefits including occlusion detection to prevent blockages, accurate readings, and the ability to notify the user when action is needed, for example, the fluid may need replacing or topped up. The sensors are robust, flexible, and reliable making them a great advancement on the traditional infusion systems that rely on gravity and require a lot more space.
Working with HITEC
We pride ourselves on our customer relationships and how we handle your application from the initial idea to the final prototype. The process begins with a collaborative discussion in which our Application Engineering team can understand your vision and what you are trying to accomplish. Using advanced modeling software we’ll create a design to meet all the required performance characteristics for your application. Prototypes are then built after a review and approval process followed by further qualification testing.
It is important that sensors are checked and tested so they can always perform at their full capacity. HITEC offers a full-service calibration laboratory located in our facility in Chelmsford, Massachusetts and is accredited by A2LA to the ISO 17025 standard. Our services include transducer repair ranging from simple wiring repairs to complete sensor remanufacturing, with reliable service and rapid turnaround. When returning the sensors back to the customer they are shipped with a NIST Traceable Calibration certificate.
We offer full customizability for your sensors so they can perform at the highest level in your application, keeping them reliable, cost-effective, and accurate.
Speak to our experts
Provide us with your information and our team will contact you
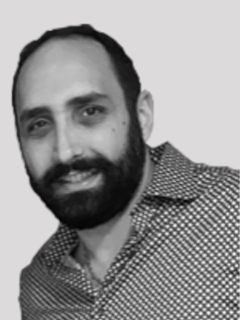
Domenic El-Achkar
Domenic El-Achkar is Director of Engineering for HITEC Sensors. He started with the company in May of 2000, as a Co-Op student while earning his B.S. in Mechanical Engineering at UMass Lowell and later earning his MBA. Domenic has developed his engineering capabilities from applications support through design, test and measurement, management, and departmental leadership. Domenic combines broad technical knowledge with a commercial mindset and good communication skills to be a very effective customer-facing technical leader. He enjoys visiting customers, developing partnerships, innovative sensor designs, and helping customers solve problems.