What is a Strain Gauge?
Strain gauges are essential sensing devices widely used in various industries to measure and quantify mechanical strain.
They play a vital role in understanding the behavior of materials under stress, ensuring structural integrity, and optimizing designs for improved performance. This article aims to provide a comprehensive understanding of strain gauges, shedding light on their fundamental principles and operational mechanisms.
How does a Strain Gauge Work?
A strain gauge is a sensor that measures the strain or deformation of an object under mechanical stress. It converts mechanical strain into an electrical signal by detecting changes in its electrical resistance. Typically made of a thin wire or metal foil, the strain gauge is attached to the object's surface. As the object deforms, the gauge stretches or compresses, altering its resistance. This resistance change is directly proportional to the applied strain. Strain gauges are widely used in industries like aerospace and automotive to monitor stress, analyze structural integrity, and optimize designs. They play a crucial role in understanding mechanical strain and enabling advancements in various fields.
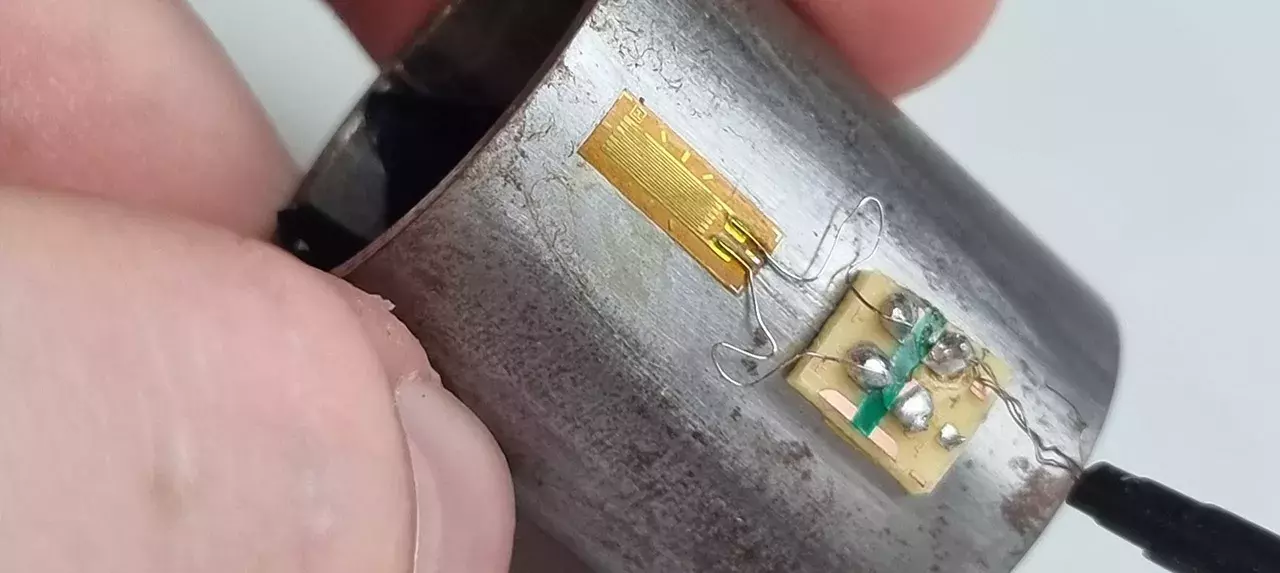
Figure 1: Example of a Strain Gauge installed on a mechanical part
What does a Strain Gauge Measure?
A strain gauge measures the strain or deformation of an object. It detects and quantifies the changes in the object's shape or dimensions under mechanical stress. By converting mechanical strain into an electrical signal, the strain gauge provides a measurable output. It operates on the principle of detecting variations in its electrical resistance as the object deforms. The gauge is typically attached to the surface of the object, and as the object undergoes stress or strain, the gauge stretches or compresses, causing a change in its resistance. As part of a Wheatstone bridge circuit, this resistance change is used to determine and quantify the applied strain on the object.
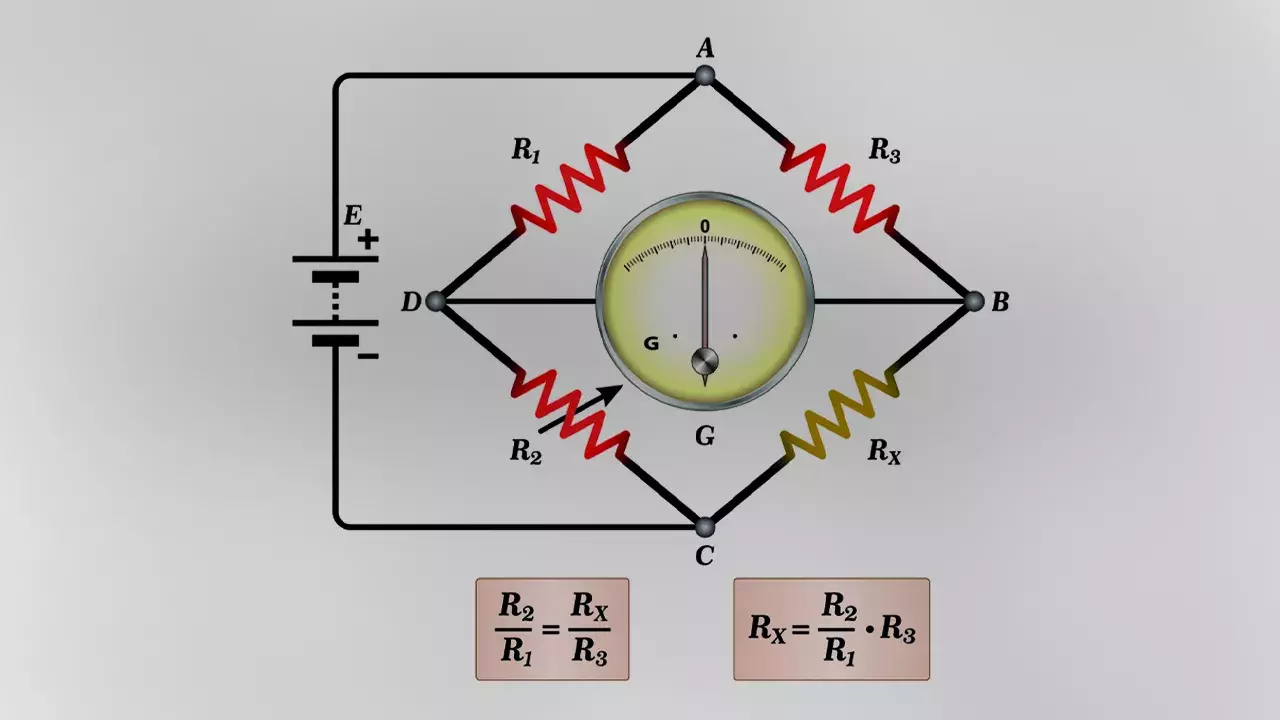
Figure 2: A Wheatstone bridge is an electrical circuit employed for the purpose of measuring an unknown electrical resistance.
Subscribe for Insights
Industry insights, trends, events and unmissable content straight to your inbox
Sign up to our newsletter to get insider access to stay up to date with all things custom strain gauge sensing
Where are Strain Gauges Used?
Strain gauges are used within load cells and industrial sensors, enabling precise measurements of force, tension, and compression. These gauges enhance safety, reliability, and performance, while providing crucial insights into material behavior and structural integrity.
HITEC Sensors specializes in the design and production of cutting-edge strain gauge-based products for a wide range of industries. Our extensive product line includes load cells, torque transducers, force sensors, specialty test systems, and advanced instrumentation.
Challenges when Installing Strain Gauges
Installing strain gauges is a vital yet intricate process that presents unique challenges for engineers and technicians in various industries. As strain gauges play a pivotal role in measuring strain and deformation, ensuring accurate and reliable installation is crucial to obtain precise data and actionable insights. Below are some of the common challenges faced during the installation of strain gauges:
Temperature
Strain gauges are sensitive to temperature variations, and changes in temperature can cause changes in the electrical resistance of the gauge itself. This can introduce measurement errors if not properly compensated for or if the temperature is not controlled during the measurement.
Environment
External factors such as humidity, moisture, vibration, or electromagnetic interference can affect the performance and accuracy of strain gauges. Adequate protection measures need to be taken to minimize the impact of these environmental factors.
Secure Bonding
Proper bonding of the strain gauge to the surface of the object is crucial for accurate measurements. Achieving a strong and reliable bond can be challenging, particularly when dealing with different materials or irregular surfaces. Improper bonding can lead to measurement errors or signal instability.
Addressing these challenges often requires expertise, careful installation procedures, calibration techniques, and consideration of environmental factors to ensure accurate and consistent strain measurements.
HITEC Sensor Capabilities
At HITEC Sensors, we pride ourselves on our exceptional capabilities in the field of strain gauges and custom sensor solutions. With decades of experience and a commitment to excellence, we specialize in providing unparalleled services for strain gauge installation, ensuring precise and reliable measurements. Our team of highly skilled engineers possesses the expertise to seamlessly integrate strain gauges into diverse applications, whether it's in the medical, aerospace, industrial, automotive, energy, or other industries.
Additionally, we offer comprehensive design and manufacturing services for custom strain gauge sensors, tailoring solutions to meet specific client requirements. From concept to realization, our dedicated team collaborates closely with clients to deliver innovative and high-performance sensor solutions that drive success.
Speak to our experts
Provide us with your information and our team will contact you
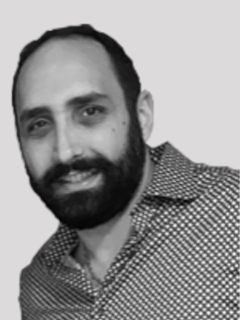
Domenic El-Achkar
Domenic El-Achkar is Director of Engineering for HITEC Sensors. He started with the company in May of 2000, as a Co-Op student while earning his B.S. in Mechanical Engineering at UMass Lowell and later earning his MBA. Domenic has developed his engineering capabilities from applications support through design, test and measurement, management, and departmental leadership. Domenic combines broad technical knowledge with a commercial mindset and good communication skills to be a very effective customer-facing technical leader. He enjoys visiting customers, developing partnerships, innovative sensor designs, and helping customers solve problems.